Few sales ordering processing cycles are planned; they just evolve over time. Management Information System (MIS) installations and the arrival of Job Definition Formats necessitate changes, but few companies have the opportunity, skills or confidence to stand back and identify how things should operate. Process streamlining is that opportunity.
Companies taking part in this course learn how to streamline their information flow, ensuring less time is wasted following ineffective processes. This makes the entire job workflow - from enquiry to delivery - a smoother, more productive and profitable process. Companies that have addressed inefficiencies in areas such as estimating, ordering, planning, artwork, delivery and invoicing have experienced benefits such as:
- Up to 23% reduction in estimating lead times
- An increased customer service capacity with no additional staff
This course focuses on targeting problem areas and applying smarter working practices. Backed up by the implementation of best practice, your staff can raise your company's standards to the best in the industry.
The programme takes place in 3 phases:
- To envisage the ideal ‘future state' process
- Drawing up current practices
- Designing a phased implementation timetable to bridge the gap realistically and with confidence
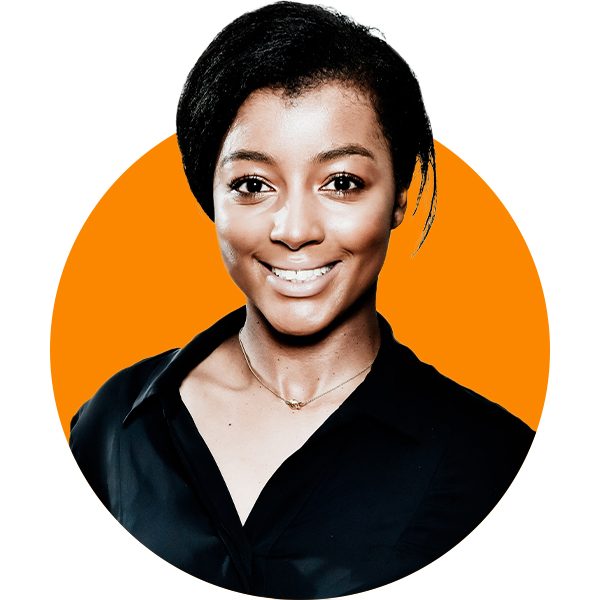
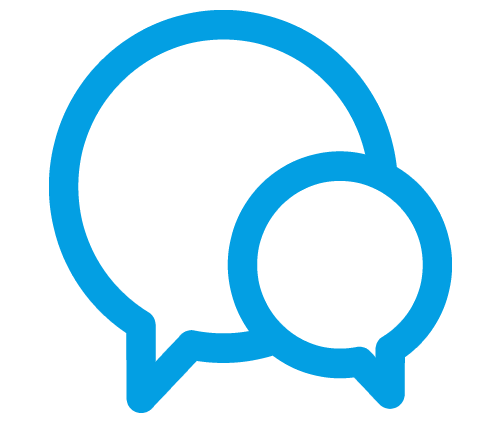
- Productivity Healthcheck Printers are under increasing pressure to deliver higher quality products at competitive prices, whilst reducing time to market
- Profit Improvement Planning (PIP) The Profit Improvement Planning Service aims to identify operational measures that can be improved to increase productivity and in turn, business profits.
- Operations Assessment The Operations Assessment is a straightforward tool which identifies what you need to do to achieve excellence.
- Total Productive Maintenance (TPM) Ever increasing pressure on deadlines means that there is never a good time for a breakdown on any of your key equipment and yet essential maintenance is often squeezed by production pressures.
- 5C/5S Workplace Organisation Implementation of 5C/5S workplace organisation techniques into your business can improve safety, productivity and customer perception.
- Press Productivity Improvement Using the experience of BPIF Process Improvement Engineers and tools designed specifically for the printing industry, this programme will bring your business measurable improvements in terms of quality, cost and delivery.
- Modular Improvement Programme Our Modular Improvement Programme is tailor-made for all UK printers that employ 25 members of staff or fewer, who are keen to raise productivity and streamline workflows.
- Bespoke Continuous Improvement Programmes Bespoke programmes are specifically tailored to meet your Continuous Improvement Strategy.
- Materials Waste Reduction This programme identifies and tackles the biggest and most easily remedied causes of waste through introducing simple measures to recognise and track waste reduction.
- Lean Manufacturing Implementation Originally based on the Toyota Production System, ‘lean' manufacturing provides a radically different way of running manufacturing processes, equally applicable to aerospace engineering or print production.
- Best Practice Publications Benchmarking your business against others is one of the most effective ways of understanding the potential for improved productivity, performance and profit.
- Why you need Process Improvement? BPIF Process Improvement provides an industry-specific and cost-effective service to help printers and packaging manufacturers to proactively improve their own productivity and competitiveness.