Eliminating machine downtime and unscheduled maintenance is one of the most important tasks for busy printers. Ever increasing pressure on deadlines means that there is never a good time for a breakdown on any of your key equipment and yet essential maintenance is often squeezed by production pressures.
Teaching your operators how to practice TPM will raise uptime for your presses and equipment, improve the quality of your products and services and enhance your operators' skills, value and craftsmanship. Since you will make less engineer callouts, you will also benefit from cost savings.
THE BENEFITS:
- Reduced downtime
- In control of your machine availability
- Boosted operator motivation and productivity by being operator-led
- Underscore the importance of maintenance to all employees
- Enhanced skills and knowledge throughout your staff
- Reduced burden on expensive engineering resource
- Increased competitiveness by reducing the cost of doing business
- Maximised savings and boosted profits
We teach a team of your key staff (both operational & engineering) to conduct TPM. This helps the team gain an understanding of the importance of preventive maintenance and Asset Care Systems. Introducing compliance measures shows the team how sustainable improvements are, ensuring buy-in and accountability for maintenance tasks going forward.
Our approach teaches your operators how to undertake preventive maintenance of even the most complex pieces of kit so that downtime is minimised and service levels are maintained. A TPM Clean, Inspect, Lubricate' regime could minimize 75% of all your machine breakdown.
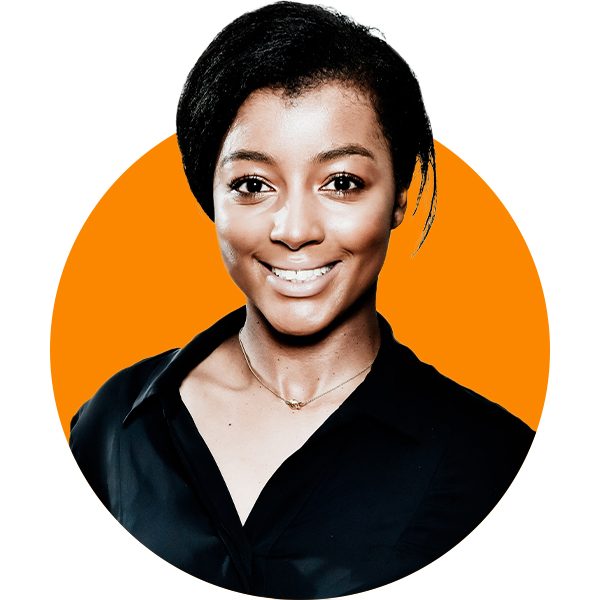
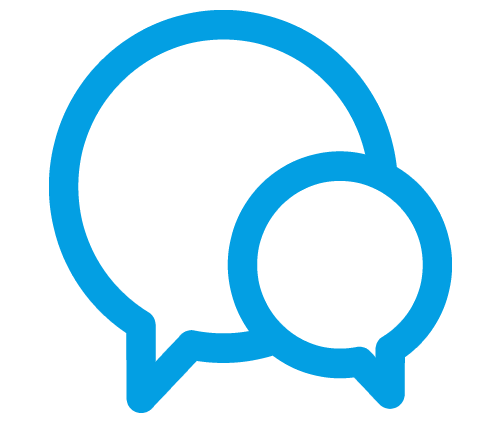
- Productivity Healthcheck Printers are under increasing pressure to deliver higher quality products at competitive prices, whilst reducing time to market
- Profit Improvement Planning (PIP) The Profit Improvement Planning Service aims to identify operational measures that can be improved to increase productivity and in turn, business profits.
- Operations Assessment The Operations Assessment is a straightforward tool which identifies what you need to do to achieve excellence.
- 5C/5S Workplace Organisation Implementation of 5C/5S workplace organisation techniques into your business can improve safety, productivity and customer perception.
- Admin & Workflow (Process) Streamlining Management Information System (MIS) installations and the arrival of Job Definition Formats necessitate changes, but few companies have the opportunity, skills or confidence to stand back and identify how things should operate.
- Press Productivity Improvement Using the experience of BPIF Process Improvement Engineers and tools designed specifically for the printing industry, this programme will bring your business measurable improvements in terms of quality, cost and delivery.
- Modular Improvement Programme Our Modular Improvement Programme is tailor-made for all UK printers that employ 25 members of staff or fewer, who are keen to raise productivity and streamline workflows.
- Bespoke Continuous Improvement Programmes Bespoke programmes are specifically tailored to meet your Continuous Improvement Strategy.
- Materials Waste Reduction This programme identifies and tackles the biggest and most easily remedied causes of waste through introducing simple measures to recognise and track waste reduction.
- Lean Manufacturing Implementation Originally based on the Toyota Production System, ‘lean' manufacturing provides a radically different way of running manufacturing processes, equally applicable to aerospace engineering or print production.
- Best Practice Publications Benchmarking your business against others is one of the most effective ways of understanding the potential for improved productivity, performance and profit.
- Why you need Process Improvement? BPIF Process Improvement provides an industry-specific and cost-effective service to help printers and packaging manufacturers to proactively improve their own productivity and competitiveness.